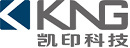
How to mix printing inks? IFM digital precise color matching system
Release Time: 2025-03-25 00:00:00.000
Digital technologies are revolutionizing the printing industry. However, ink rooms are often overlooked when offset printing plants seek ways to improve quality, reduce costs, and increase productivity. This is a significant misunderstanding, as any standardization efforts in the printing shop are wasted if the offset inks are substandard.
With the right color matching software, ink formulation can be an integral part of a color workflow that shortens cycle times and increases profitability. A digital ink formulation workflow helps offset ink rooms streamline ink measurement and formulation steps, reduce waste, and improve sustainability and cost-effectiveness.
Digital Offset Ink Room Technology
Ensuring accurate ink color matching is crucial to meeting customer color quality and consistency requirements. Inks outside tolerances increase prepress preparation time waste, defect rates, and rework, and cause costly ink waste with difficult-to-use leftover ink. Implementing digital workflows in the ink room helps reduce the potential for errors and simplifies prepress processes.
Advantages of Digital Offset Ink Formulation Workflow
Implementing digital workflows in offset ink rooms offers numerous advantages, including saving time and money and improving overall color quality, including:
- Automated ink formulation and archiving
- Reduced ink drawdowns
- Maximize leftover ink to reduce inventory
- Quickly query saved recipes from data
- Printing operators can improve print quality without deep ink expertise
- Improved repeatability between batches and jobs
- Reduced press downtime
- Reduced print setup time
Color matching software provides a solid foundation for a successful digital ink workflow. xRite InkFormulation software supports the creation, saving, approval, and querying of recipes for offset, flexographic, gravure, and screen printing inks. It can even generate new recipes using leftover inks, improving process sustainability.
12 Steps to Digital Ink Color Matching
1. Incoming Ink Inspection
Inconsistencies can exist in CMYK process inks and spot color base inks. To ensure that purchased inks are consistent and qualified, an ink drawdown can be made, allowed to dry, and measured using a spectrophotometer.
2. Define Specifications
Printing jobs typically include color specifications. This specification is usually a Pantone reference, which everyone must use as a reference target and measurement condition. It is recommended to use digital specifications for ink formulation, as they do not fade or deteriorate, and the digital file contains ink type, printing process, and substrate data.
3. Define Target Color
There are three ways to define target colors: measure physical samples using a spectrophotometer; import digital color files (CxF) from customers or the InkFormulation software library; select colors from a digital color library. These measurements and digital files will include the spectral information of the target color, which will be used to calculate the L*a*b* values.
4. Measure the Printing Substrate
Substrate color is an important consideration when formulating offset inks, as it will show through and affect the final color. Measuring it with a spectrophotometer allows it to be taken into account in the offset ink formulation calculation.
5. Establish Ink Film Thickness
Formulations should typically be defined for and verified on the offset ink room proofing press, and then fine-tuned to a specific printing ink film thickness using the software.
6. Automatically Generate Ink Formulation
The InkFormulation software will calculate suggested formulations that achieve results within the specified tolerances, listing them according to metrics such as Delta E, number of components, and spectral deviation. Once a formulation is selected, it appears in the InkFormulation software user interface.
7. Ink Drawdown Production
Mix the offset inks according to the selected formulation in a certain proportion, and then make a drawdown. When using a digital workflow based on spectral values, most customers still need physical drawdowns because digital standards give strict tolerances and specifications. This helps significantly shorten cycle times. Once the offset ink is formulated, continue to check its color accuracy by comparing it to the target. Also, ensure that the proofing press settings are as close as possible to the target press type.
8. Measure Drawdowns
Measure the drawdown from three points using a spectrophotometer and calculate the average spectral measurement. InkFormulation will compare the drawdown measurement to the target color and then calculate the Delta E. If the formulation does not meet the specifications, the InkFormulation software can correct the formulation. Reformulate the ink and make a new drawdown if necessary. In practice, digital workflows require fewer drawdowns, significantly speeding up ink preparation.
9. Save Ink Formulation
Once the formulation is determined to meet tolerances, save the formulation so that accurate ink color and weight can always be formulated in the future. Depending on the target substrate, the same color may require multiple formulations. Spectral measurements during prepress and printing help ensure color consistency and meet customer requirements.
10. Evaluate Color Matching Results
Quality control software can quickly compare the formulation to the digital color reference in the software and perform pass/fail analysis. This data helps integrate color specifications and reporting information into the supply chain workflow, allowing for efficient monitoring of printing production and real-time ink correction to avoid color errors.
11. Correct Formulation to Form a Closed Loop
When the color measurements in the flexographic or gravure printing process do not meet the tolerances and the quality control software report indicates that existing formulations cannot meet the tolerances, the data for correcting the ink formulation can be sent to the InkFormulation software with a simple button operation. The ink room can make appropriate adjustments and quickly use the new formulation for quick and efficient correction.
InkFormulation software can integrate with enhanced Management Information Systems (MIS) to close the loop on all aspects of the production workflow, from quoting to invoicing, simplifying job ink consumption estimation and reusing existing ink formulations.
12. Waste Ink Reuse
The remaining ink can be mixed evenly and used as a base ink for further color mixing, significantly reducing ink waste, saving costs, and turning waste into treasure.
Digital Offset Printing Color Management Solution
To maximize color accuracy throughout the workflow, all inks and pressroom solutions must be integrated. X-Rite solutions create a seamless, automated, and closed-loop production solution for offset printing.
1) InkFormulation software
InkFormulation uses a job-based user interface to ensure efficiency by always grouping jobs and supports information exchange with MIS/ERP systems. In addition, all ink formulations required for a given job can be associated with the job, bringing significant value to packaging service providers and ink stations.
InkFormulation software is suitable for the eXact 2 spectrophotometer and is compatible with PantoneLIVE, thus supporting the use of new digital color standards.
Color Management - Spot Ink Matching Technology
2) eXact 2 Spectrophotometer
The new eXact 2 is equipped with specific functions for ink laboratories. It features a tilting screen that is 30% larger and has double the resolution compared to the first generation, with a refreshed interface and a high-resolution camera that can identify printing defects caused by ink. Smaller printed images can be magnified for precise viewing of small areas. For ink formulation, eXact 2 also allows for non-contact measurement to minimize ink adhesion and contamination. Additionally, it has a switchable polarizing filter for formulating and verifying inks on a wide range of substrates.
Some of the pictures and texts in this site are collected and collated from the network for learning and exchange only. The copyright belongs to the original author. If you have violated your rights, please contact us to delete them in time.
More News
Kaiyin Technology - Awarded "Specialized and New Enterprise"
Kaiyin Technology, with its professional R&D and service teams, sound management system, and excellent innovation mechanism, successfully passed the enterprise self-assessment, Shenzhen municipal preliminary examination, and national ministry review procedures, ultimately winning multiple honorary titles including "Specialized and New Enterprise," "High-tech Enterprise," and "Innovative Small and Medium-sized Enterprise." The acquisition of these honors is a high recognition of Kaiyin Technology's innovation capabilities, technological R&D strength, and industry specialization, and further affirmation of the company's innovative development achievements. It marks another significant step forward for Kaiyin Technology in technological innovation and development in its specialized field.
“The colors in the sample provided by the client were gorgeous on screen, but the printed version looks like it has a grey filter applied?” - This is probably the worst nightmare for designers and printers. Color management sounds sophisticated, but the core concept is simple: “From screen to print, the colors must not deviate”. Today, we will discuss how to use X-Rite and GMG, two major “color protectors”, to ensure a perfect color match between the client's sample and the final product!
How to mix printing inks? IFM digital precise color matching system
Digital technologies are revolutionizing the printing industry. However, ink rooms are often overlooked when offset printing plants seek ways to improve quality, reduce costs, and increase productivity. This is undoubtedly a major misunderstanding, because if the offset printing ink is substandard, all standardization efforts in the printing workshop will be in vain.
Print Quality Control: Why It Matters and How to Manage It
Many printers are familiar with the print quality procedures required by some clients. For the brand, a print quality plan ensures that the printed materials meet its color requirements. Brand colors are important, and printed materials often directly represent the brand. Whether it's product labels, packaging, or brochures, print quality significantly impacts customer perception of the company. The reasons why print buyers implement print quality plans are print quality, brand color, and the complexity of achieving good print quality throughout the supply chain. While most people consider the brand when considering print quality plans, some printers also develop internal print quality plans. In all cases, the goal is the same: to ensure consistent and accurate printed products. The benefits for brands and printers are also similar - improved quality, reduced waste, increased efficiency, and saving time and money. For printers, the savings are faster turnaround times, less time, and less waste. For the brand, the benefits are brand integrity, less waste due to quality issues, and the assurance that the printer only delivers products that meet the agreed-upon requirements.


Service Hotline:
180 8888 0185
Address:
605, Building B1, Funian Plaza, No. 3, Shihua Road, Futian District, Shenzhen, Guangdong
Tel:
Fax:
Email:





Copyright ©Shenzhen Kaiyin Technology Co., Ltd 粤ICP备16126578号 SEO
Website support:300.cn ShenZhen
Mobile: 180 8888 0185
Tel: +86 755 8280 8180
Address: 305A, Floor 3, Building B1, Funian Plaza, No. 3, Shihua Road, Futian District, Shenzhen, Guangdong
Email: service@kngcolor.com
We will give you feedback in time

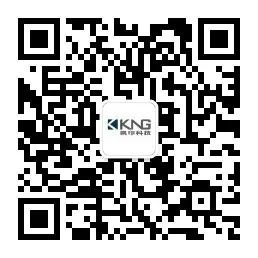
