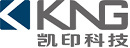
Print Quality Control: Why It Matters and How to Manage It
Release Time: 2025-03-20 00:00:00.000
Why is a print quality program important?
Many printers are familiar with some print quality procedures required by clients. For a brand, a print quality program ensures that the printed materials meet its color requirements. Brand colors are important, and printed materials often directly represent the brand. Whether it's product labels, packaging, or brochures, print quality significantly impacts customer perception of the company. The reasons print buyers implement print quality programs are print quality, brand color, and the complexities of achieving good print quality throughout the supply chain. While most people consider the brand when thinking about print quality programs, some printers also develop internal print quality programs. In all cases, the goal is the same: to ensure consistent and accurate printed products. The benefits for brands and printers are also similar - improved quality, reduced waste, increased efficiency, and saving time and money. For printers, the savings are faster makeready, time, and less waste. For the brand, the benefits are brand integrity, and fewer quality rejects, and the idea that the printer only ships products that meet the agreed-upon requirements.
Developing a Print Quality Program
A big idea in a print quality program is communication. This is the foundation for setting expectations and goals, against which all print samples are evaluated. Print quality expectations need to be clearly written and supported by documentation such as characterization data, measurement documents, and rule sets for operators producing print materials. The components of a print quality program begin with establishing clear goals and defining quality standards. During this time, print quality processes are standardized and documented, workflows are developed, and key personnel are trained. In addition to documenting goals, a key part also involves creating quality control steps, including testing procedures, monitoring, and feedback mechanisms. Finally, a data analysis and reporting plan is developed. All of this needs to be straightforward so that the print quality procedures don't unnecessarily slow down production or make the overall process overly complex. Once these standard operating procedures are developed, it's time to implement the print quality program.
Managing a Print Quality Program
The main challenge in implementing a print quality program is busyness. Minimum print quality requires knowing what you want, communicating clearly, being organized, and observing what is happening. Most people involved in design and print production have busy schedules. Unless there is a clear benefit, adding another set of tasks and attention activities is a recipe for nothing happening. Therefore, management must be behind it and provide the time and resources to implement the print quality program. As many brands and printers say, the benefits are huge, but it takes effort and time to manage. This "too busy to improve" problem can be addressed by scheduling milestones, such as weekly or monthly checks and reviews of results, and observing an overview of the print quality program and results. Without these built-in milestones, many print quality efforts are forgotten.
Print quality is not just about color. There are several print quality requirements related to good printing and fidelity to the original artwork. For good printing, we are striving to ensure that there are no significant printing defects. Examples include defects such as scuffing, mottling, scratches, hickeys doubling, and other signs of poor reproduction. Fidelity to the original artwork is also important. Certain goods have specific information that must be conveyed, and the goods must be able to be scanned and processed by retailers. Examples of these requirements include barcodes, dies, and surface finishes, as well as meeting regulatory requirements such as ingredients, instructions, warnings, and other key information that may need to be provided on the packaging. Once the program is defined, it's time to implement it. Most programs undergo a small test run before large-scale implementation. For example, an in-plant quality program might start with one press and one substrate. For a brand print quality program, the brand might start with one product line and one supplier. During the initial test and launch, the goal is to assess the feasibility of the program.
First is to check and ensure that the program is checking the truly important metrics. For in-plant projects, this might focus on attributes such as color, gray balance, and dot gain. In-plant focuses on tracking machine print characteristics as well as ink and gray balance. For brands, the program is more likely to focus on gray balance and color. The brand cares about visuals and brand color, but less about things that are non-standard across the supply chain, such as dot gain on individual machines. The most important thing is that the metrics being checked are the right metrics based on the brand's or printer's needs.
- Is the program monitoring the correct variables?
Scores need to reflect the goals of the program. In overly complex print quality programs, it's common to have jobs that have passing scores but don't match the proof. Scoring needs to capture only the important things and ignore unimportant metrics. Based on the examples above, the score should indicate the likelihood that the visuals match the proof and any key brand colors, while reducing focus on unimportant measurements. This test period is an important time to verify that the scoring system is working correctly. Often during testing (usually with top-tier operators or suppliers), failures may be intentionally created to verify different scoring situations.
- Is the scoring working correctly?
During testing, it's also important to measure the impact of the print quality program on productivity. The best programs are almost invisible, requiring little to no extra effort from the operator or supplier beyond normal quality printing. Today, the more painful examples encountered by printers often require them to manually and painfully stop the press, painstakingly measure a series of patches, make new plates, and then finally resume production. The ideal plan should be simple, fast, and provide useful feedback. During testing, work with the operator or supplier to streamline the process to be as minimally disruptive as possible. Poorly designed print quality programs can be very expensive for everyone involved.
- Is the workload of the program appropriate (i.e., not so painful that it impacts production and productivity)?
When satisfied that the program is working as designed, it's time to implement. During the process, checking the data and results will be important. Suppliers and brands will benefit from the feedback and can use this information to further optimize their processes. For printers, this might provide them with key metrics on when to recalibrate their presses to maintain print readiness as quickly as possible. For brands, this will help them understand which suppliers print best, can meet their needs, and which suppliers are worth working with more. Print quality programs are an important part of the transition from craft to manufacturing and can become an indispensable tool in your process.
Some of the pictures and texts in this site are collected and collated from the network for learning and exchange only. The copyright belongs to the original author. If you have violated your rights, please contact us to delete them in time.
More News
Kaiyin Technology - Awarded "Specialized and New Enterprise"
Kaiyin Technology, with its professional R&D and service teams, sound management system, and excellent innovation mechanism, successfully passed the enterprise self-assessment, Shenzhen municipal preliminary examination, and national ministry review procedures, ultimately winning multiple honorary titles including "Specialized and New Enterprise," "High-tech Enterprise," and "Innovative Small and Medium-sized Enterprise." The acquisition of these honors is a high recognition of Kaiyin Technology's innovation capabilities, technological R&D strength, and industry specialization, and further affirmation of the company's innovative development achievements. It marks another significant step forward for Kaiyin Technology in technological innovation and development in its specialized field.
“The colors in the sample provided by the client were gorgeous on screen, but the printed version looks like it has a grey filter applied?” - This is probably the worst nightmare for designers and printers. Color management sounds sophisticated, but the core concept is simple: “From screen to print, the colors must not deviate”. Today, we will discuss how to use X-Rite and GMG, two major “color protectors”, to ensure a perfect color match between the client's sample and the final product!
How to mix printing inks? IFM digital precise color matching system
Digital technologies are revolutionizing the printing industry. However, ink rooms are often overlooked when offset printing plants seek ways to improve quality, reduce costs, and increase productivity. This is undoubtedly a major misunderstanding, because if the offset printing ink is substandard, all standardization efforts in the printing workshop will be in vain.
Print Quality Control: Why It Matters and How to Manage It
Many printers are familiar with the print quality procedures required by some clients. For the brand, a print quality plan ensures that the printed materials meet its color requirements. Brand colors are important, and printed materials often directly represent the brand. Whether it's product labels, packaging, or brochures, print quality significantly impacts customer perception of the company. The reasons why print buyers implement print quality plans are print quality, brand color, and the complexity of achieving good print quality throughout the supply chain. While most people consider the brand when considering print quality plans, some printers also develop internal print quality plans. In all cases, the goal is the same: to ensure consistent and accurate printed products. The benefits for brands and printers are also similar - improved quality, reduced waste, increased efficiency, and saving time and money. For printers, the savings are faster turnaround times, less time, and less waste. For the brand, the benefits are brand integrity, less waste due to quality issues, and the assurance that the printer only delivers products that meet the agreed-upon requirements.


Service Hotline:
180 8888 0185
Address:
605, Building B1, Funian Plaza, No. 3, Shihua Road, Futian District, Shenzhen, Guangdong
Tel:
Fax:
Email:





Copyright ©Shenzhen Kaiyin Technology Co., Ltd 粤ICP备16126578号 SEO
Website support:300.cn ShenZhen
Mobile: 180 8888 0185
Tel: +86 755 8280 8180
Address: 305A, Floor 3, Building B1, Funian Plaza, No. 3, Shihua Road, Futian District, Shenzhen, Guangdong
Email: service@kngcolor.com
We will give you feedback in time

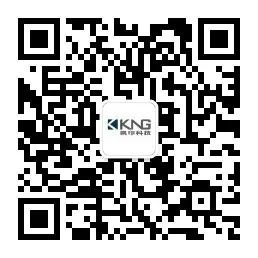
