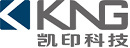
It's time to replace your CTP equipment: 3 reasons you need to know
Release Time: 2025-03-16 00:00:00.000
Upgrading your computer-to-plate (CTP) equipment is a significant investment. However, such an upgrade can open your business to a world of new opportunities. In a fast-paced industry like printing, equipment replacement is often a last resort. Computer-to-plate (CTP) equipment is no exception. Profit margins are shrinking, and technological and business trends are changing rapidly. By proactively upgrading to the latest CTP model, you can stay ahead of the curve, seize new business opportunities, and, importantly, save money.
Three Key Reasons to Replace Your CTP Equipment
1. Aging Equipment
If you haven't upgraded your CTP equipment in the past 7-10 years, you're likely facing capacity constraints. While your current equipment may still function, the increasing speed of printing often outpaces its ability to produce plates to meet output demands.
Kodak CTP is known for its quality, durability, and reliability, but any CTP equipment is a complex system. Older equipment becomes less reliable and more prone to problems. After years of use, components from the engine to the thermal heads, lasers, sensors, and automated controllers can all degrade. After 10 years of use, sourcing spare parts for your direct imaging device will also become increasingly difficult.
Older machines also present other risks. Security is a concern for businesses of all types and sizes, and keeping up with new operating systems and security patches is more important than ever. Outdated CTP equipment can create vulnerabilities and pose serious security threats, putting customer data, your reputation, and even your business at risk.
2. Your Business Heavily Relies on Offset Printing; New Equipment is Key to Growth
Offset printing offers long runs and excellent quality and efficiency. However, it also demands high-quality plates. As an offset printer, you may process tens of thousands of plates annually—a high throughput demand that older, manual CTP equipment struggles to meet.
Your existing CTP equipment may get the job done, but does it empower your business to thrive in a world of opportunity? With the latest CTP equipment, the platemaking process is fully automated, highly streamlined, and requires minimal manual intervention for plate loading, imaging, or sorting. You can deliver more plates to the pressroom faster, fully meeting business output and quality goals for plate volume and variety. New equipment reduces labor and energy costs, minimizes waste, and enhances cybersecurity for offset printing businesses.
New equipment can also help you stay ahead of evolving industry trends. For example, with the rise of personalized printing, many print customers want solutions that support frequent design changes. As this trend intensifies, the ability of offset printers to leverage advanced CTP solutions to increase efficiency becomes even more critical. Every offset business wants to grow, and new CTP equipment will help ensure you can meet increasing demands.
Your existing CTP equipment may get the job done, but is it keeping up with market demands? Does it empower your business to thrive in a rapidly changing world? CTP technology has advanced significantly since your last purchase, and the platemaking process has become increasingly sophisticated.
New innovations enable higher throughput, better output quality, and a smaller footprint. Automated options, including remote monitoring capabilities, save time and labor. Combined with energy-saving features, simplified operation, and reduced errors and waste, automation can save you significant costs. But that's not all. The more plates you can automatically load, image, and unload, the more jobs you can process daily, boosting your revenue potential.
New CTP technology also features new imaging technologies. You can achieve finer detail in your output, even at faster speeds, ideal for fine art printing, microprinting, security printing, and halftone printing. The ability to easily achieve various demanding printing effects will set you apart and allow you to meet the diverse needs of a large customer base. The entire platemaking process is also more environmentally friendly. For example, the latest Kodak Sonora and Magnus platesetters use 3% less energy during imaging than our previous models and 95% less than comparable direct imagers on the market. Kodak direct imagers are also perfectly paired with Kodak Sonora XP process-free plates, further reducing the environmental impact of platemaking. In short, upgrading empowers you to easily meet existing customer needs and exceed their expectations, allowing you to discover new growth opportunities. Ultimately, you will see a significant return on your investment.
3. Your Existing CTP Equipment May Be More Costly
Unexpected CTP downtime can quickly increase unpredictable costs. This includes obvious expenses like repair and parts costs—and eventually replacement costs. Service contracts also increase in price for older equipment because older equipment requires more frequent checks and diagnostics. While Kodak provides excellent support to its customers, the maintainability of equipment does become more challenging as machines age and technology becomes obsolete. Parts may be more expensive if the older equipment platform is incompatible with newer models.
Beyond that, you also need to consider downtime, which leads to lost revenue and increased costs. If the direct imager fails, a critical piece of the printing process is rendered ineffective. All of these factors add up, and the total cost may end up being higher than purchasing new equipment—monthly payments may actually be lower.
Businesses face many unpredictable threats, uncertainties, and pressures, leaving no room for error. Investing in advanced platemaking technology and modernizing your platemaking process can streamline workflows, reduce business risks, and ultimately give you peace of mind.
The Ideal Solution Awaits
A good solution is not simply tinkering with a user's existing configuration; it's about making revolutionary improvements and enhancements. By investing in new CTP equipment, Kodak continues to lead industry change. Kodak's new equipment can now deliver plates to the printing department faster and reduce labor costs, eliminating costly plate remakes. Kodak's award-winning technology is suitable for businesses of all sizes, and its automation level can be customized to your needs.
Kodak offers a range of new and refurbished CTP equipment to help you achieve plate-making levels you never dreamed possible—from the entry-level Kodak Trendsetter manual CTP to the high-end, scalable Kodak Magnus Q8000T Plus model with multi-tray plate loading. New CTP solutions can improve your existing workflow in various aspects, such as capacity, efficiency, growth, and profitability. Saying goodbye to old equipment may be quite different from what you expect in terms of cost; it may actually lower your costs.
Some of the pictures and texts in this site are collected and collated from the network for learning and exchange only. The copyright belongs to the original author. If you have violated your rights, please contact us to delete them in time.
More News
Kaiyin Technology - Awarded "Specialized and New Enterprise"
Kaiyin Technology, with its professional R&D and service teams, sound management system, and excellent innovation mechanism, successfully passed the enterprise self-assessment, Shenzhen municipal preliminary examination, and national ministry review procedures, ultimately winning multiple honorary titles including "Specialized and New Enterprise," "High-tech Enterprise," and "Innovative Small and Medium-sized Enterprise." The acquisition of these honors is a high recognition of Kaiyin Technology's innovation capabilities, technological R&D strength, and industry specialization, and further affirmation of the company's innovative development achievements. It marks another significant step forward for Kaiyin Technology in technological innovation and development in its specialized field.
“The colors in the sample provided by the client were gorgeous on screen, but the printed version looks like it has a grey filter applied?” - This is probably the worst nightmare for designers and printers. Color management sounds sophisticated, but the core concept is simple: “From screen to print, the colors must not deviate”. Today, we will discuss how to use X-Rite and GMG, two major “color protectors”, to ensure a perfect color match between the client's sample and the final product!
How to mix printing inks? IFM digital precise color matching system
Digital technologies are revolutionizing the printing industry. However, ink rooms are often overlooked when offset printing plants seek ways to improve quality, reduce costs, and increase productivity. This is undoubtedly a major misunderstanding, because if the offset printing ink is substandard, all standardization efforts in the printing workshop will be in vain.
Print Quality Control: Why It Matters and How to Manage It
Many printers are familiar with the print quality procedures required by some clients. For the brand, a print quality plan ensures that the printed materials meet its color requirements. Brand colors are important, and printed materials often directly represent the brand. Whether it's product labels, packaging, or brochures, print quality significantly impacts customer perception of the company. The reasons why print buyers implement print quality plans are print quality, brand color, and the complexity of achieving good print quality throughout the supply chain. While most people consider the brand when considering print quality plans, some printers also develop internal print quality plans. In all cases, the goal is the same: to ensure consistent and accurate printed products. The benefits for brands and printers are also similar - improved quality, reduced waste, increased efficiency, and saving time and money. For printers, the savings are faster turnaround times, less time, and less waste. For the brand, the benefits are brand integrity, less waste due to quality issues, and the assurance that the printer only delivers products that meet the agreed-upon requirements.


Service Hotline:
180 8888 0185
Address:
605, Building B1, Funian Plaza, No. 3, Shihua Road, Futian District, Shenzhen, Guangdong
Tel:
Fax:
Email:





Copyright ©Shenzhen Kaiyin Technology Co., Ltd 粤ICP备16126578号 SEO
Website support:300.cn ShenZhen
Mobile: 180 8888 0185
Tel: +86 755 8280 8180
Address: 305A, Floor 3, Building B1, Funian Plaza, No. 3, Shihua Road, Futian District, Shenzhen, Guangdong
Email: service@kngcolor.com
We will give you feedback in time

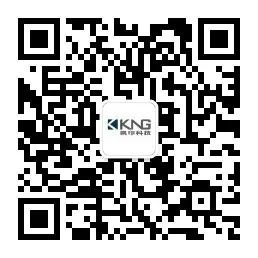
